海上筑基显身手
探访全球最大打桩船“二航长青”号
中央纪委国家监委网站 沈东方
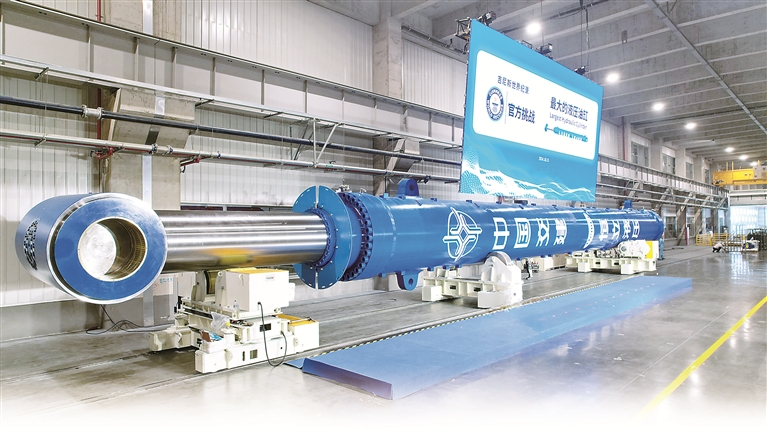
“二航长青”号的主油缸由我国自主研发,是全球最大液压油缸。
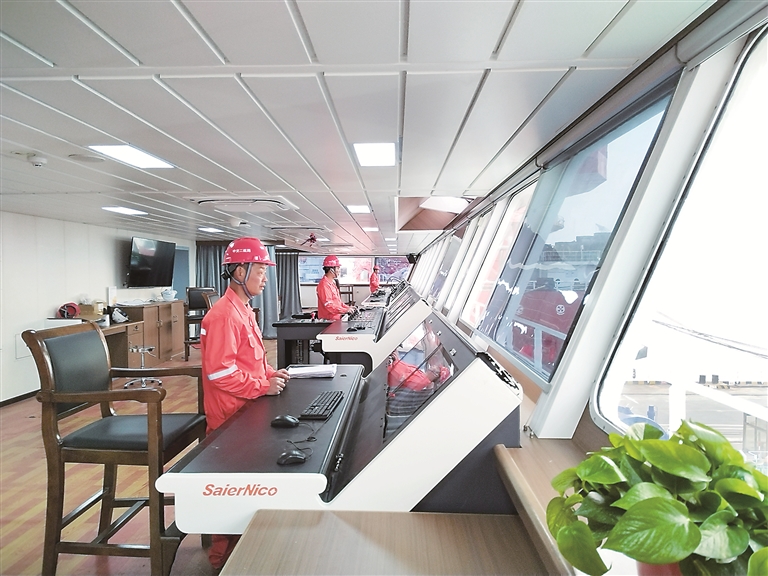
“二航长青”号工作人员在驾驶室查看智能作业辅助决策系统。
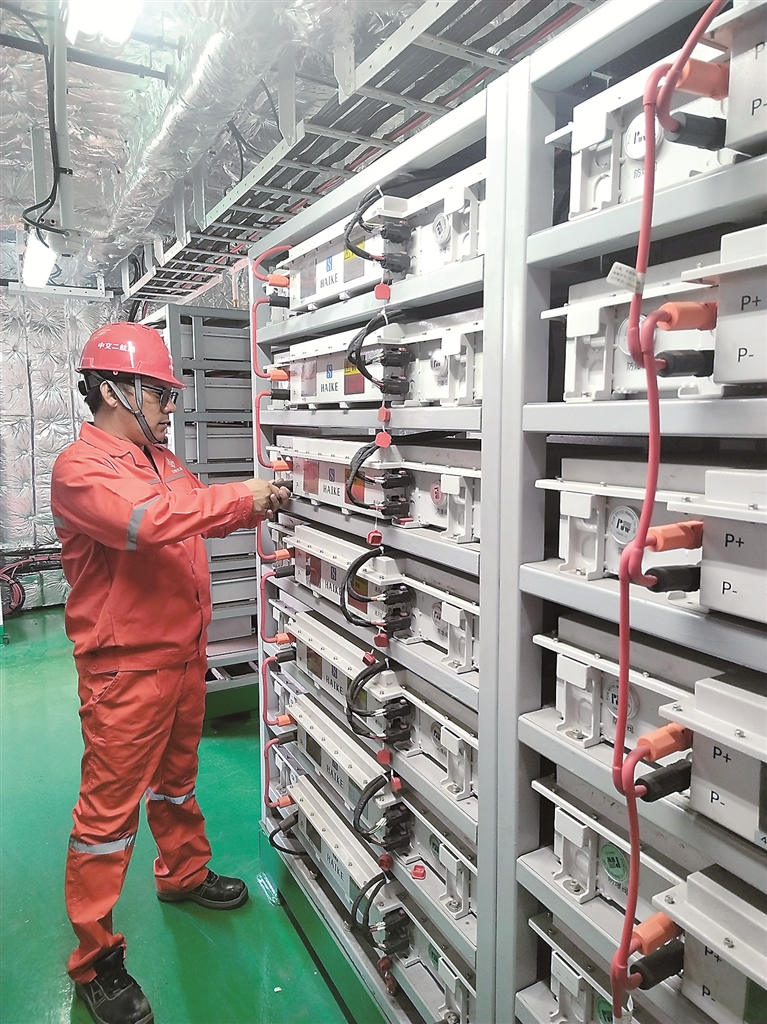
“二航长青”号工作人员在电池间检查锂电池应用情况。
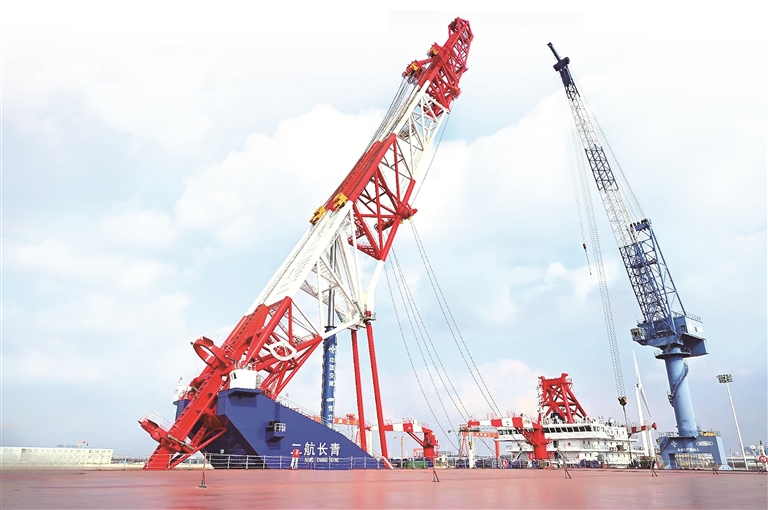
“二航长青”号。 中交二航局供图
一艘红蓝相间的巨轮停靠在岸边,150米的桩架高耸入云……全球最大打桩船“二航长青”号前不久在江苏启东海工船舶工业园交付。在这艘超大型打桩船研发过程中,研发团队取得多项关键核心技术成果,我国在海洋工程装备制造领域实现新突破。
在海洋重大工程建设中,打桩船扮演着怎样的角色?要把巨大的桩基稳稳打入海底,需要具备哪些条件?超大型打桩船的自主研发过程中有哪些故事?让我们一同探访“二航长青”号。
世界桩架最高、吊桩能力最大的打桩船,可打最大桩重700吨、直径7米的桩基
在海洋工程的施工建设中,需要先把多根钢管打入水底形成桩基础,为工程建筑提供稳固的支撑。打桩船就是承担这项任务的专用装备之一。
随着海洋资源的开发和利用日益受到重视,打桩船的应用范围不断扩大,它不仅广泛应用于桥梁、码头等传统基础设施的建设,还涉及海上风电、岛礁开发等新兴领域。
除了应用领域的不断扩展,桩基越打越深也是一大趋势。中交二航局技术中心二级副总工程师刘修成向记者介绍,以前打桩船工作的水深约为20多米,随着海洋工程的建设逐渐走向深远海,现在打桩船工作的水深会达到50—60米,这也对打桩船的性能提出更高要求。
以一根钢筋为例。“海水越深,需要插入海底的钢筋长度就越长。在同等直径下,长钢筋比短钢筋更容易弯折。为了保证钢筋的坚固稳定,我们需要增大钢筋的直径。而这样一来,钢筋自重相应提升,打桩船把它‘提起来’再‘扎下去’所需要的力量也就更大。”刘修成说。
打桩船一般由船体、桩架、油缸三部分组成,船体是平台,桩架是支撑。无论是远看还是近观,“二航长青”号最引人注目的都是其150米高的桩架,竖起来有50层楼那么高,这样的高度在全世界都是首屈一指的。
拥有高耸桩架的“二航长青”号是一个庞然大物。它总长130.5米,型宽40.8米,型深8.4米,桩架高度150米,可打最大桩重700吨、直径7米的桩基。
与这一组参数密切相关,“二航长青”号是世界桩架最高、吊桩能力最大、施打桩长最长、抗风浪能力最强的打桩船。
这些参数的背后,是精密的计算和长远的考量。
“如果从效率、经济、安全等多方面考虑,打桩船的一系列参数其实并不是越大越好。”刘修成介绍,船是有寿命的,如果设计的参数太大,造价就会相应提升,这艘打桩船可能直到退役都还没有发挥出最大的效能,就像“杀鸡用牛刀”一般浪费了资源。与此同时,参数也不能太小,得考虑到海洋工程未来的发展,比如桥梁码头、海上风电未来可能会需要怎样性能的打桩船,在确定主参数的时候预留一些提前量,保证其在今后的十多年内依然站在行业领先位置。
据记者了解,目前“二航长青”号正在做最后的调试整备。新春伊始,它将在世界最长跨海高速铁路桥——杭州湾跨海铁路大桥建设中一展身手。不仅如此,“二航长青”号还将驶向大洋彼岸的巴西,参与萨尔瓦多跨海大桥的建设。
自主研发全球最大液压油缸,牢牢掌握打桩船“心脏”的核心技术
油缸是打桩船的“心脏”,是最重要的部分。它可为打桩船桩架提供推力,帮助桩架精准调节角度。在大油缸的帮助下,打桩船不仅能打垂直桩和斜桩,还能在通过桥梁时降低身高“躺平”,以便顺利从桥下穿过。
2024年10月15日,中交二航局牵头研发的全球最大打桩船主油缸在江苏常州下线,这也是“全球最大液压油缸”。该油缸重385吨,直径近2米,总长28米,重量、直径、长度均为全球第一,其额定推力达5000吨,相当于一次性可举起1000头重5吨的非洲象。
油缸V组密封等关键部件曾经是我国海洋工程装备制造领域的短板,长期受制于国外技术。“二航长青”号主油缸自主研发成功,打破了我国大型打桩船主油缸核心部件长期依赖进口的局面,展示了我国在大型海洋工程特种装备制造领域的技术创新能力。
在研发过程中,中交二航局联合国内产业链头部企业和知名高校,形成了产学研用体系,分别开展油缸整机和关键部件研发。通过组建体系化、任务型创新联合体,从研究理论、仿真分析和实验全方面攻关,相继研发了国产密封圈、国产轴承润滑垫、激光熔覆耐腐蚀材料等,以关键核心技术成果保障油缸顺利下线。
打桩船的打桩能力与油缸推力成正比。大型油缸的外观看起来是个大圆缸筒,如果把油缸比作注射器,那么缸筒就是外壁,活塞杆是推杆,各部件相互配合进行工作。“二航长青”号主油缸的缸筒与活塞杆总重305吨、设计直径大,曾给研发生产带来前所未有的挑战。
“受重力影响,缸筒与活塞杆在生产中极易发生弯曲变形,‘二航长青’号主油缸超出了国内外现有油缸加工能力。”中交二航局总工程师张永涛介绍,为此,油缸主体结构研发团队新建了配套生产线。在活塞杆制造方面,新建了国内最大的25米车磨一体床,可一次定位完成车、磨、抛等精加工工序,能减少多次装夹造成的误差。在缸筒制造方面,新建了超大缸筒加工成套装备,采用多段拼接等工艺,使缸筒总直线度误差不超过0.3毫米。
海水盐分高、腐蚀性强,即便是不下水的船上部件,也面临着防腐蚀的考验。“比如,平常家里的空调能用十几年,但是打桩船上的空调只要两三年就会出现严重生锈情况。”张永涛举例道。
保证油缸稳定运行的关键零部件——密封圈也是如此。
由于海洋作业环境复杂,油缸长时间高温高压运行,易导致密封圈损坏,而一旦密封失效,油缸推力变小,就无法保证动作准确精密。密封圈研发团队用性能优异的夹布橡胶制作密封圈样件,把样件放到模拟油缸设备中进行测试。通过严格测试的国产密封圈首次在大型打桩船油缸上使用,并实现零泄漏。
“智慧大脑”提高打桩精度和安全性,混合动力系统进一步降低碳排放
海上行舟,面临波涛汹涌。在起起伏伏的海浪中,打桩精度和作业安全如何保证?
船的尺寸越大,抵抗波浪的能力也越强。“海浪形成起伏的波峰和波谷,波峰代表最高点,波谷则代表最低点。当一艘船足够长的时候,它就可以压住多个波峰波谷,上下晃动的‘跷跷板效应’也不会那么明显。此外,海浪一般只在一定深度的水层波动,增加吃水深度也可以减少波浪对船的影响。”中交二航局副总工程师杨秀礼介绍,“二航长青”号总长130.5米,结构吃水深度可达6米,其庞大的身躯保证了在水中的相对平稳状态。
除了加强硬件实力外,“二航长青”号还配备了“智慧大脑”,帮助它在工作中安全又高效。
杨秀礼告诉记者,“以前,我们都是通过肉眼观察判断当前的海况是否能够进行打桩。现在,船上配备了基于风浪流随船感知的智能作业辅助决策系统,该系统可以通过扫描波面实时收集波浪参数,为船长提供是否能进行沉桩作业的决策依据,还能实时在线监测打桩过程环境安全。”
海底打桩作业对垂直度和精度的要求非常高,比如,桩基的垂直度偏差需要控制在1/200以内,平面偏位必须小于25厘米。一旦打歪了或者偏了,不仅影响未来建筑物的承重能力,更容易带来安全隐患。
为此,“二航长青”号上配备了远海星站差分功能打桩定位系统,能在深远海实现厘米级的定位精度,并提供精度误差超限预警。
不仅如此,“二航长青”号还配备了打桩作业管理系统,在打桩作业时,该系统可自动判断作业工序,记录作业时长,用于工效统计、能耗分析等打桩效果评估。该系统还能自动记录沉桩数据,建立关联地质资料、桩参数和沉桩记录等相关信息的大数据库。
绿色节能也是这艘超大型打桩船的一大特点。“二航长青”号在行业内首次应用配置超级电容的柴电混合动力直流组网技术,进一步提高了燃油经济性,降低了碳排放。
“简单来说,这种技术能提高用电设备的运行效率,尽可能让每一滴油都发挥出最大价值。”杨秀礼解释道,“二航长青”号通过配置超级电容,与柴油动力系统相结合,形成了混合动力系统。超级电容具有瞬间大容量充电和放电的优点,可以在短时间内提供或吸收大量电能,从而平衡柴电动力系统的负荷波动,提高整个系统的能效和稳定性。